Aerofloat’s expertise in wastewater treatment for large scale food and beverage manufacturers is on full display at the ready-meals manufacturer Beak & Johnston’s newest $100 million production facility.
The state-of-the art 10,500 sqm facility, unveiled in October in Arndell Park, Sydney, has an Aerofloat wastewater system in place, more specifically, Aerofloat’s Aero V-DAF 30 system, with 30m3/hr treatment capacity.
Michael Anderson, general manager, engineering and projects, Aerofloat, said it was the company’s first time working with Beak & Johnston, but that the company’s experience helped with the consultation process.
“Our past work with ready meal companies gave us insight into the variability and seasonal conditions of a wastewater plant,” said Anderson.
“This experience helped us analyse and design the wastewater treatment process for City Kitchens.”
Aerofloat’s expert experience creating bespoke wastewater treatment solutions across Australia is another advantage, given the variety of requirements.
“The project involved creating a trade waste plant for Sydney water compliance,” said Anderson.
Wastewater standards are different from state to state, with Victoria having some of the more relaxed regulations. This is due to the state having the largest sewerage treatment plant in the country which can withstand input from food and beverage providers without as much input from wastewater treatment, but input, nonetheless.
Aerofloat can apply the required standards and regulations to each job, no matter where in the country it is, to ensure its clients not only meet, but exceed the requirements.
This is helped along by the company ensuring its engineers assist in both the design and construction of water treatment plants using a variety of options for clarification, filtration, and disinfection.
The team undertakes extensive consultation with a client to ensure the design is the best one for the space and requirements, namely ensuring treatment systems will run effectively, are future proofed, and produce effluent that meets discharge requirements.
Some of the things which need to be looked at include incoming feed quality, which will dictate the water treatment design, along with the best way to integrate other systems into the design.
Aerofloat also takes sustainability and efficiency seriously, ensuring the final design is both.
Anderson said Aerofloat undertook its usual hands-on approach, which plays a key role in developing solutions that are unique to each customer.
“We conducted due diligence on the wastewater based on the products City Kitchens would be producing,” he said.
“The process included a pump station for wastewater collection, a treatment room where large food particles are screened out, a balance tank for mixing, aeration, and pH correction, and a reaction tank for coagulation and flocculation.
“This leads to a dissolved air flotation system, using our newly developed Aero V-DAF 30 system. 30m3/hr treatment capacity.”
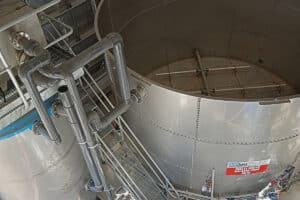
Dissolved air flotation (DAF) is the physical chemical separation technique employed to remove suspended solids and fats, oils, and grease from the wastewater.
Aerofloat has patented DAF technology in its AeroDAF, which has combined proven traditional dissolved air flotation principles with world-first patented design elements to make a truly innovative product which is perfectly tailored to the food industry.
Some of the benefits and features of the wastewater solution include the patented scum removal, which reduces maintenance time, coupled with a unique double hopper design that is self-cleaning, eradicating the need for mechanical scrapers.
This also creates a more cost-effective solution for food and beverage manufacturers and producers. Aerofloat’s AeroDAF is also compact in design, making it easier to fit into a small footprint, saving space to produce goods for the client.
“Different clients require different DAFs, depending on their requirements and we take pride in doing our due diligence to provide the best wastewater treatment solution,” said Anderson.
“We look at data around waste streams and gain a deep understanding of a client’s internal processes, and we use that sound wastewater data to select the right DAF.
“We can process to the 200-litre per minute speed, or we can slow it down. This system is ideal because creates a lot of room for expansion alongside the company without having to be replaced any time soon.”
Aerofloat’s AeroDAF solutions can, and are, developed for the individual needs of clients. From compliance to space, output, and growth expectations. As shown by the Beak & Johnston wastewater solution.
“The whole plant was a custom solution, including the wastewater plant layout and all mechanical, electrical, and process components,” said Anderson.
“We also had to accommodate other equipment in the plant room, like fire suppression pumps.
“We also factored in future growth. For example, sizing the balance tank for peak hourly and daily flows.
“The system is also designed to be efficient and adaptable for different types of food production.”
“Our history with ready meal centres really was crucial. It gave us confidence and made it easier to sell our solution to City Kitchens.”
As environmental and sustainability standards continue to become stricter, food manufacturers need to ensure they collaborate with a trusted wastewater treatment provider who can guide them through the best solution for their business.